The Day When Investing in Safety Pays Dividends
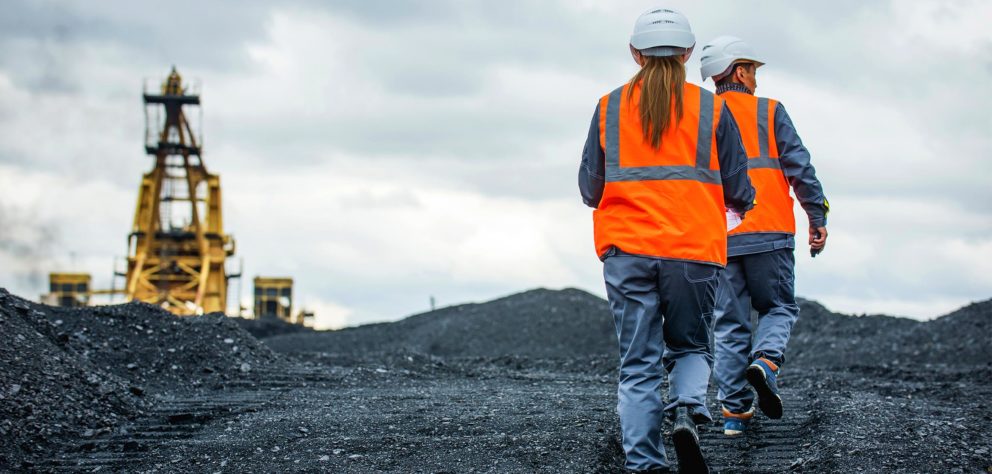
Mention safety and many people think of training and protective clothing. What is easily overlooked is the potential risk brought about by the failure of lower quality equipment.
A mining contractor friend of ours shared this first-hand account of an equipment failure incident and the levels of safety that gave it a happy ending.
While this isn't a site we are involved with, we thought it was a compelling safety share.
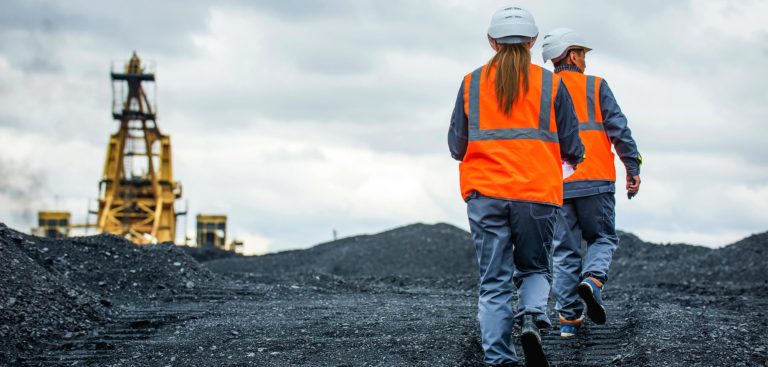
"We are high-pressure water blasting (HPW) the internals of a tank used to store sulfuric acid. There are three of us on the team. One co-worker, the outside spotter for confined space entry, is standing outside the tank. I am standing at the entrance door to spot for Working at Heights and (HPW). My supervisor is in a scissor lift cage 6 metres up the sidewall. We rotate the job of blasting to share the workload and manage fatigue. The two of us at ground level are part of the safety procedure you follow when a team member is working at heights in a scissor lift.
At the end of the blast hose, my supervisor is holding a big high-pressure water blasting gun. He is blasting the acid and rubber debris off the walls with the HPW. It is spraying out of the nozzle at 160 litres per minute. He is wearing a harness and full personal protective equipment. (PPE)
As I'm watching, there is a loud bang, like a shotgun blast. My supervisor is thrown the full length of the scissor lift cage. I run into the tank to see if he's alright. He is a big bloke, and he is not moving. I run back out of the tank and tell the outside spotter to get the ERT, Emergency Response Team. Back inside, my supervisor still isn't moving. I unplug the scissor lift and manually lower him back to the ground.
A deadly hole blew out in the hose right where it connects to the gun. There is a protective sock over the hose, but the water blew right through. It was running about 30,000 psi - roughly 2,200 bar of pressure. That water blast hit my supervisor in the chest.
I thought the blast had killed him.
After a while, he finally comes around. He stirs but he still can't talk because the impact of the water has badly winded him. On the front of his apron, I can see where the impact has hit his chest. It is a fist-sized mark that nearly goes right through it. It is a rated Kevlar; it's like bullet-proof. It's part of your PPE for working with high-pressure water. I can see that it has saved his life. Later, we decide that the recently inspected hose must have been faulty. It goes back to the manufacturer for investigation.
As for our team, we were doing everything right on that day. We'd followed every safety procedure to the letter. I got to witness how protective gear saves lives. I got a masterclass in why the procedures are there. I saw my own training kick in just when I needed it.
Nobody died because all the right procedures were in place. We'd ticked all the boxes. Without that, it could have easily gone the other way. You've got to respect high-pressure water. You've got to give close attention to what you're doing. Take the time to double-check everything. Follow the safety procedures and your training. That's the most important thing. I was pretty clear about all that before this incident. I can assure you, I'm even clearer now."