Review: Pump Maintenance Training
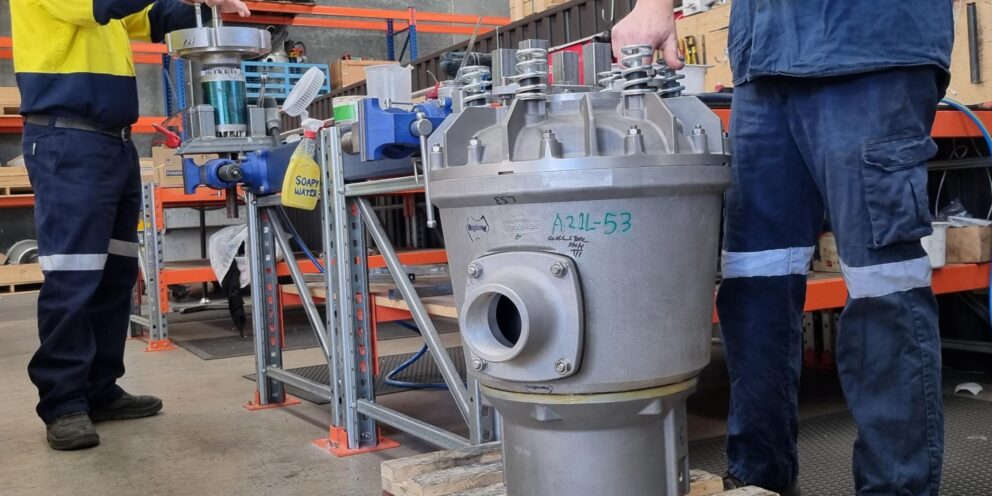
Paul Burke is an underground electrician, part of a contracting team servicing one of WA's largest underground mines. He works on long haul drill rigs, jumbo drills rigs and all the dewatering pumps. He services or rebuilds pumps and performs maintenance on underground electrical equipment, including fibre networks. Paul reviews the content and value of PumpEng pump maintenance training.
You recently had some pump training from PumpEng. Why did you decide to do that?
We've got 22 pumps up here owned by the mine, and we need to maintain them. I needed the knowledge to repair these pumps. It's pretty tricky as I'm not a pump fitter as such. I'm an electrician. The electrical part is fine, but the mechanical seals and the wet end part of the pump need more knowledge than I have had. PumpEng trained me to take apart the pump and put a pump together again most efficiently and correctly.
Can you describe the training process? How long did it take, and where did you do it?
I went to the PumpEng head office in Bibra Lake for two days. The training process was rebuilding a 20 kW pump. The trainer, Gavin, showed me how to put a pump together from scratch. He carefully taught me the correct procedure and ensured I understood what was necessary. During the process, I realised we needed to be doing a lot of things correctly. Such as, when you put a mechanical seal in, you're supposed to put oil on the faces, but we weren't doing this. That is pretty critical.
I learned how to test the pump once I'd put the mechanical seals in. To ensure that the mechanical seal is functioning correctly, you need to put in the air pressure and ensure that it holds that pressure over time. If you don't, and it isn't holding, and you put a whole pump together again, you will blow your mechanical seal, and your pump will fail. Then you are back at square one. You're going to pull the thing apart again and waste time when you could be doing more productive work. It became clear that sparkies on site know the electrical side, but we need the training to look after the pumps efficiently.
What was your trainer like?
Gavin was very thorough. He patiently answered all my questions. He would start doing something, and I would ask, "Why did you do that?" Knowing the why behind tasks deepens your understanding and makes remembering easier. He was good at explaining how he does it, why, and when to do it. Such as what tests to do, how to do them, and how much pressure you need to get things right.
I ended up taking videos of it with my phone. I can refer back to them if I need to because there's a lot to it. A pump has many different parts, which all need to work well. Yes, my trainer was excellent.
What did you learn about the importance of pressure testing? How would you sum it up?
To sum it up, once you've put those mechanical seals on, you have to put some air pressure in them, and the air pressure has to hold for a certain amount of time. If it drops a little bit, which I've seen, I thought maybe that would be okay, but it's not. You've got to check it's sealed and put it back together again. I learned from that pressure testing process that you must leave it for half an hour to ensure it is holding the correct pressure. I used only to leave it for five minutes, sometimes less.
Torque Nuts and Bolts
Onsite people think it's just a pump and should be fine. Another example of training is understanding the torque on the nuts. 60 newton-metres. And the top and tail bolt, 80-newton meters. I was amazed at the precision that makes a difference. The trainer used a torque gun that you set to a specific setting, which will tighten up the nut to that setting.
Oils
We covered what sorts of oils to use and the correct place to use them. I learnt that they use drain holes, and this is pretty interesting. They use the drain hole to fill the oil rather than the actual fill hole. I didn't know because I've been putting it in the oil hole, which you naturally would. You wouldn't put it in the drain hole. The trainer explained that putting it in the oil hole means it bubbles up, and you don't get as much oil in. There's an airlock, and he showed me why. As you pull it apart, you're supposed to fill the oil in the drain hole. Here is something simple that I didn't even know. I was doing that wrong. It was significant finding out the correct way to do things and why it is crucial the next time I deal with a pump.
What were the other valuable insights that you took away?
Gloves
He had some special gloves you could use, the heat gloves. We haven't had the right gloves to handle it when you heat the bearing, grab it, and then try to put it in the pump. So there was a safety aspect to this as well. I got to see the more appropriate protective gear, so I know what to arrange for the crews onsite.
Pressure Gauge Testing
The pressure gauge tester we have onsite could be better. The trainer gave me the details for the pressure gauge testers so we can buy better ones for ourselves. Next time we build a pump on-site, I'll use the same gear they are using.
Do you think the training will help you be more efficient in what you do?
The Correct Process
Yes. It means being able to do the process steps correctly so that you don't have to go back and do other work again later. I know we weren't testing mechanical seals properly and weren't putting this oil on the mechanical seals, either.
Getting Testing Right
The training helps me to test at the proper stages. We still need to do a couple of tests up here. Having the right gear means we can test in the right way. This all comes down to how safe it is because manual handling is reduced. They're very heavy pumps. If you don't have to take it apart when you've done it incorrectly, there's less manual handling, and you're more efficient. Fewer breakdowns mean less risk because they're heavy and can hurt your back.
Getting things done a bit slower and correctly the first time is better. Rather than rip it apart, which some of us have to do because we're not trained for this type of work, this is the best training we can have. Now I know this is how I've got to do it. There is far less frustration.
Now that I've had the training, we could have been more professional in our approach to pump maintenance. W didn't know any better. When you get the training, you know better after that.
What would you say to someone new to pumps about the value of getting this training?
It would be best if you got the sparkies to do this training before they start pulling a pump apart. I've seen so many people come and go from our site. They haven't got any idea because we all think we can do something. They pull it apart, put it back together, and it doesn't work, and they get frustrated. The pattern repeats when the next guy comes along. Every new Sparkie needs to get this training. It is going to mean a lot less frustration. Maybe if they are more skilled and confident, they'll even stay longer.
Is there anything else you would like to add?
People didn't do much training before because they've got to do this on their break. I feel grateful to PumpEng for helping arrange this training for me. I got so much out of it.
I've got more knowledge, and knowledge is power, right? I have a less frustrating day at work if I seal a pump. I know the equipment we need and the system to follow.
I did think about a manual, but again, the problem is that people wouldn't read it during their break. It's their time off. But I find you've got to do it. If it were up to me, I'd put people on the PumpEng course first, and then you would send them up to the site. They'd be more productive from day one. My day at work and quality of work is much better than the person who hasn't had the training. Their day at work is a lot harder. They have to struggle to work out how they put this pump back together. I don't. I've had the training and am much more confident and in control of my work.