Gold Mine Adopts The PumpEng Way
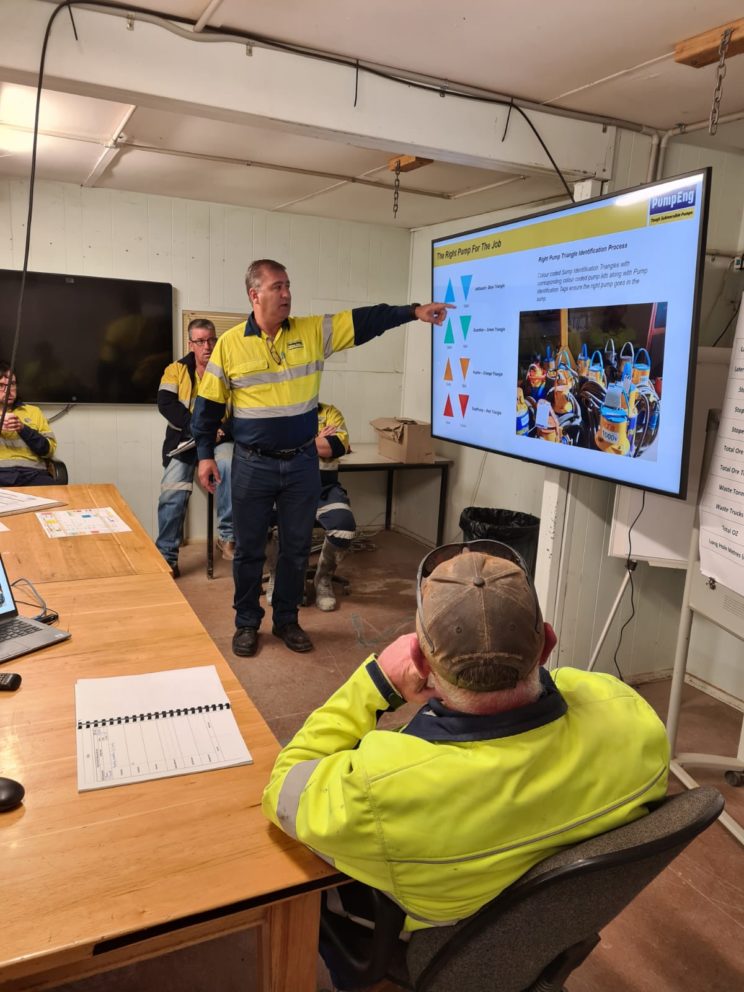
A WA gold mine has adopted The PumpEng Way as a site-wide strategy to boosting mine productivity. This holistic approach has several key elements.
PumpEng has designed a colour coded guidance system to ensure that the right pump is used for the job. Sump sites are inspected to identify the best match for the demands of a particular sump, with the correct dynamics from a fluid point of view.
With the most appropriate pump identified, the next challenge is to communicate clearly with busy maintenance crews. Their correct choice of dewatering pump will mean that pump failure is less likely to be a cause for delays in production on that site.
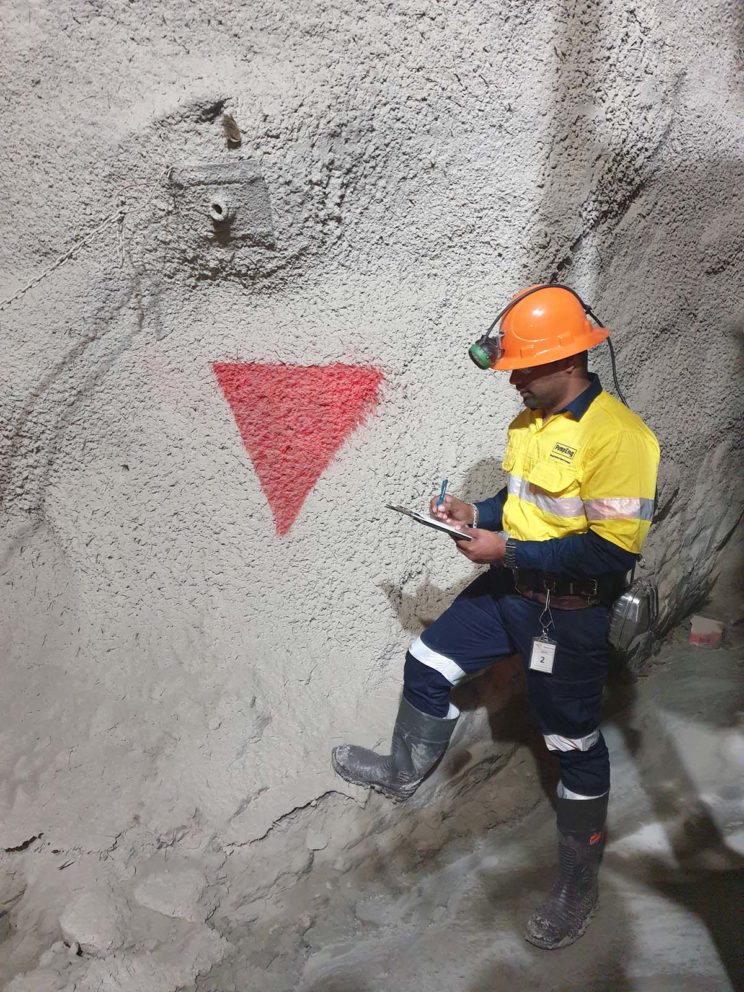
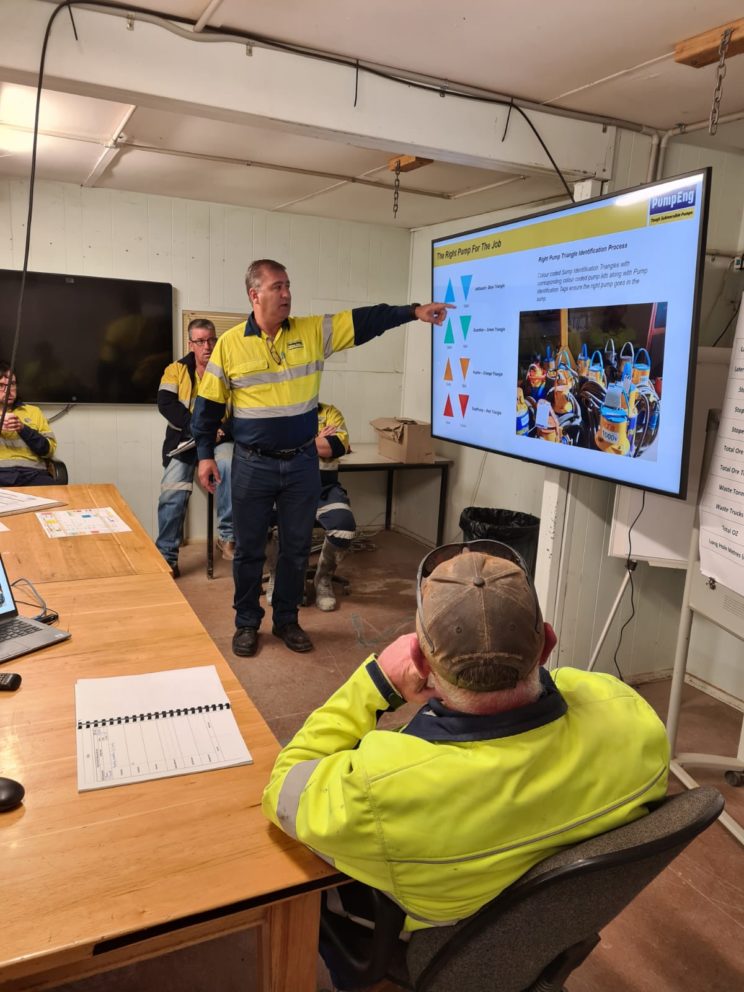
PumpEng has developed colour coded triangles to assist maintenance crews to quickly identify which pump is needed. This is helpful as many crew members have limited training and experience with pumping dynamics. The coding makes it easy for them to get pump choice right every time.
After an initial site inspection, PumpEng paints coloured triangles on the mine wall beside each sump. The triangle colour matches the lid colour of a dewatering pump models. The direction of the triangle matches the size of the pump required for that location. Each pump is tagged to show its match to a specific triangle direction. For example, a triangle pointing down is the smaller pump size, an 8 kilowatt. The triangle pointing up is a higher head size, the pump model with more volume.
Maintenance crews can send a specific request to the service crew for a "red pump with a downward triangle" instead of, "there's a pump on the service, grab it because any pump will do." Crews are trained by PumpEng to understand that this correct matching will mean a significant increase in mean-time-between-failure.
Managers will notice a reduction in costs. Crews will notice less maintenance events. Overall there will be more continuous production. Operational pumps don't cost anything and don't impact production.
The PumpEng Way includes processes of data analysis, continuous improvement and the ongoing training. PumpEng aims to reduce frustration for mine managers and help provide a good day at work for everyone on site.